ADAS Data Capture & Storage Computing Solutions
ADAS Data Capture and Storage Computers (Advanced Driver Assistance Systems)
Autonomous vehicles and those with Advanced Driver Assistance Systems (ADAS) need a lot of data to train the algorithms that help with driving and avoiding accidents. This data, gathered from real-world situations, is essential for training these systems effectively. Capturing this data, which comes from cameras and sensors, demands powerful computers with strong processors and ample high-speed storage. The more data these systems gather, the better they become at object detection and navigation.Vehicles with features like automatic braking, collision protection, and autopilot rely on high-resolution cameras, Lidar, ultrasonic and sonar sensors, GPUs, and other sensors to understand their surroundings. To fine-tune these ADAS systems, test vehicles are fitted with special data capture and storage computers that can handle the information from the vehicle's cameras and sensors.
Since these cameras and sensors can generate up to 4TB to 5TB of data per day, having a system with sufficient storage is vital. This data is too large to be sent to the cloud effectively, so it's stored directly on the vehicle. This calls for an edge computing solution onboard the vehicle, with the necessary performance and storage capacity to manage this massive amount of data.
C&T provides a range of AI Edge Inference Computers in their RCO-6000-RPL Series, expertly designed to be used in vehicles for collecting and storing data from cameras and sensors. These ADAS data capture computers are highly customizable, featuring powerful 12th and 13th-generation Intel Core processors (i3, i5, i7, i9), ensuring efficient handling of high-resolution data from cameras and sensors. Additionally, these computing solutions offer extensive storage options to accommodate large volumes of data.
For instance, these computers can be equipped with a variety of storage devices, including multiple M.2 NVMe SSDs, U.2 NVMe SSDs, standard SATA SSDs, and HDDs. Some models can support up to 8x U.2 NVMe SSDs or 2x internal SSDs or HDDs, along with 2x hot-swappable SSDs or HDDs using the SATA protocol. This flexibility and extensive storage capacity make C&T’s vehicles data capture and storage computers exceptionally capable of handling the terabytes of sensor data produced by autonomous vehicles and those with ADAS features.
How Much Data Do ADAS Equipped Vehicles Generate?
Vehicles outfitted with autonomous features or ADAS can create substantial data, typically ranging from 4TB to 5TB each day. This high volume is due to the cameras and sensors installed in these vehicles, including sonar, ultrasonic, LiDAR, and GPS sensors. For example, the cameras in ADAS-equipped vehicles can generate 20-60 MB/s, radar about 10KB/s, LiDAR between 10-70 MB/s, and GPS approximately 50KB/s. When you tally up these figures, it's clear that such a vehicle can generate up to 130MB of data every second, which equates to roughly 8GB per minute.
Image Source: Synopsys
Autonomous vehicles that spend about 10 hours on the road each day can produce up to 4.8TB of data daily. The volume of data generated largely depends on the number and type of sensors and cameras installed in the vehicle. The higher the resolution of these cameras and the greater the number of sensors and cameras in use, the more data is produced. However, this can vary as some systems might use fewer resources, while others could be equipped with more, affecting the total amount of data generated.
What Happens to ADAS Data That is Captured and Stored?
The data captured and stored by Advanced Driver Assistance Systems (ADAS) is crucial for enhancing the performance of these systems. When ADAS uses machine learning (ML) or deep learning (DL), the data collected by AI edge inference computers is used to train the models. This training improves the system's ability to recognize objects, people, lane markers, and street signs, especially in new environments.
During the training phase, artificial neural networks learn to identify and classify objects similarly to humans. Training these models demands significant processing power, typically carried out in data centers with the aid of GPUs. GPUs are preferred for this task due to their ability to process more data simultaneously, thanks to their higher core count compared to CPUs. Once trained, these models are then deployed in vehicles to perform real-time analysis on unfamiliar data, environments, and objects. The quality of this training directly impacts the algorithm's effectiveness in object identification and vehicle navigation.
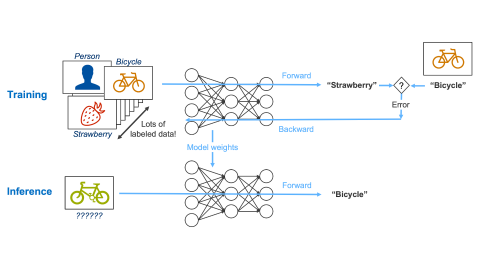
Deep Learning Training - Image Source: Intel
To effectively train models with the vast amounts of data from test vehicles, these vehicles need to be equipped with hardened AI edge computers. These computers are designed to connect with and collect data from vehicle cameras and sensors. They come with powerful processors and robust storage solutions capable of handling the terabytes of data generated.
Using powerful edge computers is essential because much of the data needs to be stored and processed locally. This is due to the challenges and high costs associated with transmitting terabytes of data via cellular connections. Cellular networks typically don't offer the necessary upload speeds for such large data volumes, and the cost of sending this data over cellular networks is prohibitively expensive for most organizations.
Consequently, AI edge inference computers play a crucial role in data management. They store the data locally, occasionally sending important processed information to the cloud through cellular connectivity. However, the bulk of the data is usually offloaded at a centralized location, often involving the physical removal of hard drives for manual data transfer to a central computer. This approach balances the need for immediate data processing with the practicalities and costs of data transmission.
Advanced Driver Assistance Systems (ADAS) Ruggedization & Features
1. Fanless Design
When choosing an ADAS computer for capturing and storing data from vehicle cameras and sensors, opting for a fanless design is advisable. Fanless industrial computers are particularly suitable for vehicular deployment, as they are less susceptible to damage from dust, debris, and other small particles. The absence of fans in these computers prevents such particles from entering and harming the internal components.

Additionally, the fanless construction means the system does not rely on fans for cooling. This is a significant advantage because fans often cause malfunctions in electronic devices, including computers. By eliminating this common failure point, fanless computers offer enhanced reliability and durability, making them a more robust solution for the demanding conditions encountered in vehicle operations.
2. Shock and Vibration Resistance
When selecting an ADAS PC for handling vehicle sensor data, choosing a system that offers robust shock and vibration resistance is important. AI edge inference computers are designed to withstand tough conditions, featuring 50Gs of shock protection and 5GRMs of vibration resistance, in line with MIL-STD-810G standards. This resilience is essential for vehicle deployment, which often encounters frequent shocks and vibrations while traveling on various road surfaces.

C&T enhances the durability of its ADAS computers by adopting a cable-free design within the system. Eliminating cables reduces the number of moving parts, thereby decreasing the potential points of failure. This approach leads to a more reliable and long-lasting solution, well-suited for the demanding environment of vehicular operations.
3. Wide Operating Temperature Range
One more important point is to choose one that can withstand extreme temperatures, given the diverse environments vehicles may encounter. C&T’s AI edge inference computers are ideally suited for this purpose, with an operating temperature range of -25⁰C to 60⁰C. Their fanless design and components specifically selected for wide temperature ranges ensure optimal performance in challenging conditions, from the scorching heat of the Mojave Desert to the freezing cold of a New York winter.
Unlike regular desktop computers, which are designed for temperature-controlled indoor environments and typically operate between 5⁰C and 40⁰C, Premio's rugged edge computers are built to endure more extreme temperatures, making them a reliable choice for in-vehicle deployments. This durability is built into the system, eliminating the need for additional hardware to cope with temperature fluctuations.
4. Power Input Compatibility
A wide power range also is very important. This ensures the system can operate effectively using a vehicle's power source. C&T's edge computing solutions are designed with this versatility in mind, capable of adapting to various power input scenarios. Additionally, C&T's systems are equipped with multiple power protection features, including overvoltage protection, surge protection, and reverse polarity protection, enhancing their reliability and safety for vehicular use.
5. Power Ignition Management
Choose one with power ignition management. C&T's AI edge inference computing solutions are equipped with this feature, enabling them to recognize when a vehicle starts or stops. This triggers a boot delay when the vehicle powers on, and a delayed shutdown when turned off, ensuring the system completes its tasks without data loss or corruption. Additionally, this feature prevents the system from draining the vehicle's battery when it's turned off, enhancing its efficiency and reliability.
6. CANBus Capable
CANBus is a communication protocol used in vehicles to relay messages between various components. By integrating with the CANBus system, organizations can access crucial vehicle information like speed, engine RPM, throttle position, steering angle, tire pressure, and more. It's important to choose a system connecting to the CANBus network for data collection, essential for developing advanced driver assistance systems. For instance, C&T’s AI edge computers can connect to a vehicle’s CANBus system to gather this data.
While CANBus is prevalent in most modern vehicles, there's a growing trend toward adopting automotive ethernet (100 Base-T1). This shift is driven by the need for higher bandwidth in connected, autonomous, and self-driving vehicles, signaling a future change in-vehicle data communication technologies.
7. Wired & Wireless Connectivity
Edge AI inference computers offer a range of wired and wireless connectivity options for internet access and connection to various devices. They typically include Dual RJ45 Gigabit ports for fast data transfer and connection to high-resolution cameras and sensors.
These systems are equipped with Wi-Fi 5 or Wi-Fi 6 modules for wireless connectivity, providing flexibility in connection speed and range. Wi-Fi 6 enhances connectivity with technologies like Mu-MIMO and OFDMA. Mu-MIMO allows simultaneous connection to multiple devices, increasing network throughput, while OFDMA enables communication with multiple clients at once by dividing Wi-Fi channels into smaller units.
Given the mobility of vehicles, cellular connectivity is also crucial for transmitting critical data to the cloud. Edge AI computers often come with Dual SIM sockets for redundancy, ensuring reliable connectivity even in remote areas or with weak signals. Additionally, they can be configured with Bluetooth for simple, reliable connections to sensors and IoT devices, although it offers limited range and speed compared to Wi-Fi and wired options.
Bottom Line
The key takeaway is that ADAS-equipped vehicles rely heavily on vast amounts of data to develop and refine advanced driver assistance systems for safe operation and accident prevention. To effectively capture and store this data, these vehicles require AI edge computers. These computers must have powerful multi-core processors and substantial storage capacity to handle the terabytes of data generated daily by each vehicle. ADAS computers also feature a rich array of I/O connections, enabling them to link up with numerous sensors and cameras for comprehensive data collection and storage. For any queries or guidance in choosing an ADAS data capture and storage PC, edge computing experts are available to help you find a solution tailored to your specific needs..